The Significance of Clamps in Post-Processing An Essential Tool for Precision and Stability
In the world of manufacturing, engineering, and craftsmanship, the role of a clamp cannot be overstated, especially when it comes to post-processing tasks. A clamp, that seemingly simple device, is an indispensable tool that ensures precision, stability, and safety during various stages of workpiece manipulation. This article delves into the essence of clamps in post-processing, exploring their functionality, types, and the benefits they bring.
Post-processing refers to the series of operations carried out after the initial manufacturing phase, such as finishing, assembly, or quality control. During these stages, clamps play a pivotal role in securing workpieces firmly in place, allowing craftsmen to work with accuracy and efficiency.
Clamps come in a myriad of designs, each tailored to specific applications. From C-clamps and F-clamps for heavy-duty tasks to spring clamps and bar clamps for more delicate operations, their versatility is a testament to their utility. In post-processing, they ensure that materials remain steadfast while being sanded, painted, glued, or machined, preventing any unwanted movement that could compromise the final product's integrity.
One of the key advantages of using clamps in post-processing is the precision they facilitate. By holding workpieces securely, they allow artisans to execute intricate cuts, bends, or welds with unparalleled accuracy. This is particularly crucial in industries where tolerances are tight, such as aerospace or medical device manufacturing.
Moreover, clamps contribute significantly to workplace safety. They prevent accidental slips or falls, reducing the risk of injury to operators and damage to the workpiece They prevent accidental slips or falls, reducing the risk of injury to operators and damage to the workpiece
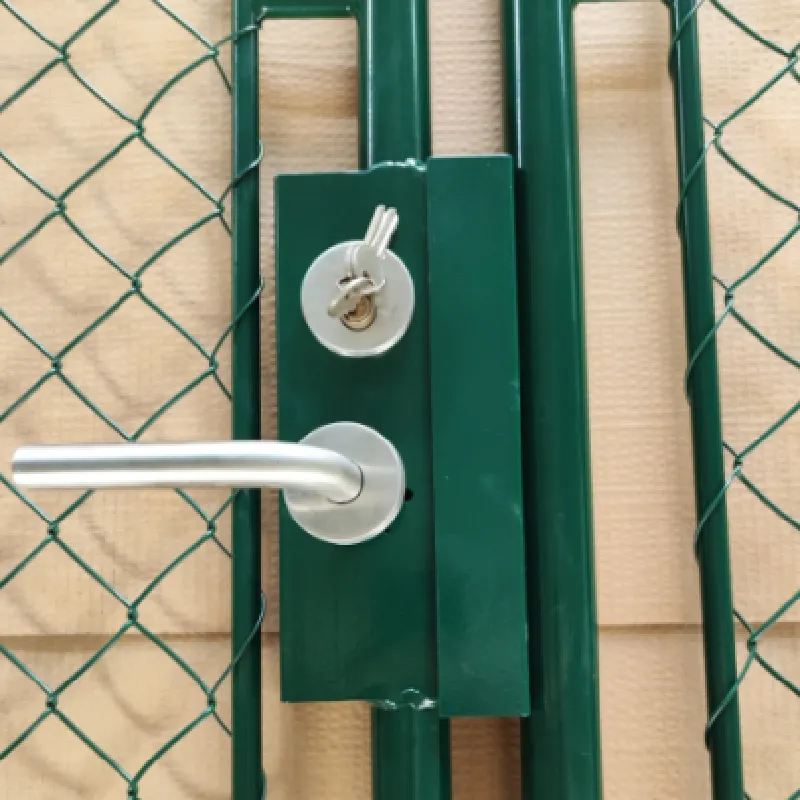
They prevent accidental slips or falls, reducing the risk of injury to operators and damage to the workpiece They prevent accidental slips or falls, reducing the risk of injury to operators and damage to the workpiece
clamp for post. They also alleviate the need for manual holding, freeing up hands for other tasks and minimizing the strain on workers.
The durability and robustness of clamps make them a cost-effective investment. High-quality clamps, often made from durable materials like cast iron or aluminum, can withstand the rigors of daily use and last for years, providing a consistent return on investment.
In addition to their practical applications, clamps also offer a level of customization. With adjustable pressure and various jaw shapes and sizes, they can accommodate a wide range of workpiece dimensions and shapes, making them adaptable to diverse projects.
In conclusion, the clamp's role in post-processing is not merely ancillary but integral. It is a silent partner in the creation of precision-engineered products, ensuring that every detail is executed to perfection. Whether it's a woodworking project, metal fabrication, or industrial assembly line, the clamp's importance cannot be underestimated. As technology advances, so too do clamps, with innovative designs emerging to meet the evolving needs of modern manufacturing. Thus, the clamp, humble yet essential, remains a cornerstone of post-processing, fostering precision, efficiency, and safety in countless workshops worldwide.